- What's in Your Smart Home?
- Posts
- What's in Your Smart Home? - Hempcrete
What's in Your Smart Home? - Hempcrete
What's in Your Smart Home? - Hempcrete
Hempcrete? Smart? Absolutely! Smart because of the energy savings over the lifetime of your home and of course it’s a renewable resource that’s great for the environment.
Hempcrete is a bio-composite building material made from the stalks of the hemp plant, combined with a lime-based binder. It is a sustainable, non-toxic, and carbon-negative material that has gained popularity in the construction industry for its numerous benefits.
One of the primary benefits of Hempcrete is its high insulation value, which can lead to significant energy savings over the life of a building. It is also lightweight, fire-resistant, and has excellent acoustic properties. In addition, Hempcrete is mold-resistant, pest-resistant, and breathable, which helps regulate humidity levels in the building, improving indoor air quality.

Third Space Commons at UBC | iPhone image: © 2023 Rod Mountain
I recently had a chance to attend the newly built Third Space Commons at UBC. Third Quadrant Design is UBC’s first green building design team and they have constructed a net zero building on campus which includes an 18” thick wall of Hempcrete providing an estimated insulation factor of R40.
This building, located on the UBC campus, will serve three distinct purposes over its lifetime.
First, Third Quadrant deconstructed and adaptively reused materials and systems from an existing single-family home on the UBC campus, showcasing the feasibility and importance of reuse in today's building market.
In its second life, Third Space Commons serves as a net-zero energy and carbon single-family home for the Solar Decathlon competition. The space itself is adaptable to the needs of a family during different times of the day. Design decisions are guided by five key principles: carbon minimalism, circularity, flexibility, living lab, and resilience.
Finally, after the competition, the building will have a third life as a living lab and student-collaboration space for UBC students. The space’s flexibility will allow for both formal and informal interactions in the form of a classroom and commons area. Integrated building systems such as rainwater collection, mixed-mode ventilation, and smart controls ensure that students have a ‘living lab’ to learn about, experiment and test climate-resilient solutions.

Third Space Commons at UBC | iPhone image: © 2023 Rod Mountain
What about heating? Well this is smart too! Heating is provided by electric radiant floor heating, selected as a low carbon alternative to heat pumps, while fresh air is provided by natural ventilation or a heat-recovery ventilator (HRV) for mechanical ventilation. The specified Oxygen8 Ventum unit has the ability to provide high flow rate (600 cfm) at very high heat recovery rates of up to 87%. In the future, the HRV may be retrofitted with a HEPA filter to support air quality studies at UBC.
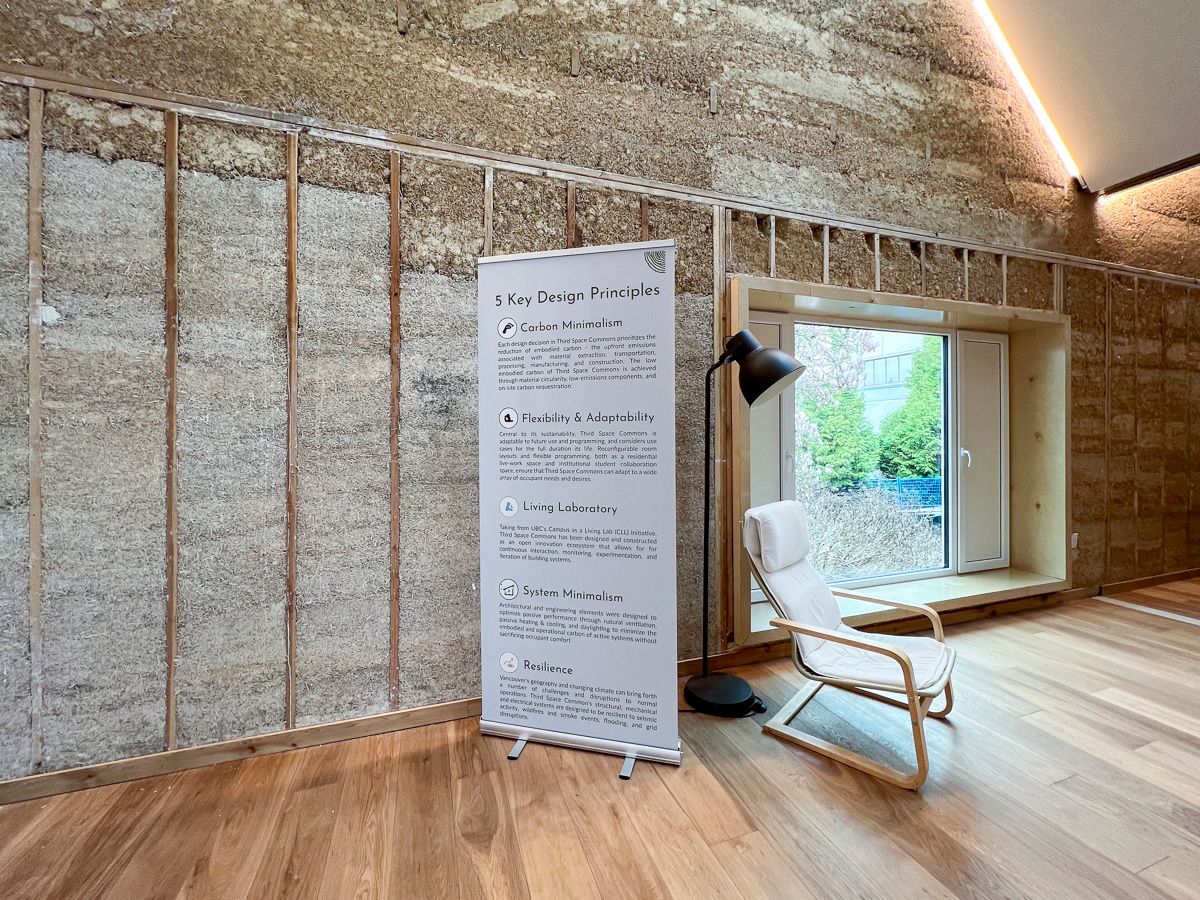
Third Space Commons at UBC | iPhone image: © 2023 Rod Mountain
The five key design principles for the building were Carbon Minimalism, Flexibility & Adaptability, Living Laboratory, System Minimalism, and Resilience.
The project included build partners Third Space, Daniel Family Foundation, Bosa Properties, and Corix.
https://third.space / @thirdspaceproperties
https://bosaproperties.com/en/ @bosaproperties
Other Design and construction partners included;
RJC Engineers https://www.rjc.ca @RJC_Engineers
RDH Making Buildings Better https://www.rdh.com @RDHBuildings
Introba https://www.introba.com @Introba_Inc
Stantec https://www.stantec.com/en @Stantec
Dialog https://dialogdesign.ca @DIALOG
Ledcor https://www.ledcor.com @LedcorGroup
Hall Constructors https://www.bdhall.ca
Houle https://www.houle.ca @houleelectric
UCS Forest Group https://www.ucsforestgroup.com @UpperCanada_FP
Accoya https://www.accoya.com @Accoya
Institutional Sponsors;
UBC Sauder School of Business
The University of British Columbia
U.S. Department of Energy Solar Decathlon
UBC Civil Engineering
UBC Engineering Design Teams
Wall Raisers;
Lanefab Design/Build https://www.lanefab.com @LanefabDesignBu
Pitt Meadows Plumbing https://pittmeadows.net @pittmeadowsplumbing
Urban One https://urbanonebuilders.com @urbanonebuilders
Intracorp https://intracorphomes.com @Intracorphomes
Polygon https://polyhomes.com @polygonhomes
BC Helical Piles https://www.bchelicalpiles.com
Oxygen8 https://oxygen8.ca @oxygen8canada
Cultivators and Seed Growers;
Dick’s Lumber https://dickslumber.com @dickslumber
Soprema https://www.soprema.ca @sopremacanada
VREC Solar https://www.vrec.ca @vanrenew
Siga https://www.siga.swiss/ca_en @siga_canada
Columbia Skylights http://www.columbiaskylights.com @Columbia_Sky
Fluor https://www.fluor.com @FluorCorp
GeoScan https://www.geoscan.ca @geoscan_subsurface_surveys
West Coast Home & Truss https://www.westcoasttruss.ca @westcoasttruss
Terrafibre https://terrafibre.ca @Terrafibre
Graymont https://graymont.com/en @graymont_lime
Fenstur Windows https://www.fensturwindows.com @fenstur
Passivehouse Canada https://www.passivehousecanada.com @passivehousecan
Wescondoors https://www.wescondoors.com @wescondoors
Hempworks Canada http://www.hemp-works.ca @hempworkscanada
BGC Engineering https://www.bgcengineering.ca @bgcengineering
Super Save Group https://supersave.ca @SuperSaveGroup
Onni Group https://www.onni.com @onnigroup
Armstrong Fluid Technology https://armstrongfluidtechnology.com @ArmstrongFT
Lionsgate Scaffolding https://www.lionsgatescaffolding.com/#/
Sunbelt Rentals https://www.sunbeltrentals.com @SunbeltRentals
EllisDon https://www.ellisdon.com @EllisDon
Underhill https://underhill.ca @UnderhillGeomat
AIBC https://aibc.ca @AIBCconnected
i3 Building Science & Consulting https://www.i3bsc.org
Griff Building Supplies https://www.griffbuildingsupplies.com
Randy & Claudia Findlay
Third Space Commons, is one of Canada’s first institutional spaces designed to have near-zero embodied carbon. Virtually every material, construction technique and design element of the project was chosen for its ability to lower or even capture carbon emissions. The foundation of the building is made of reusable steel piles, and the team chose light wood framing rather than engineered wood for the majority of the building’s structure. The team also sourced materials sustainably, prioritizing the adaptive reuse of materials from other construction sites in Vancouver where possible. The Third Quadrant Design team accounted for the carbon impact of nearly every material that went into the project, including its electrical, heating and ventilation systems. The team received the inaugural B.C. Embodied Carbon Award for Small Building Construction by the B.C. Carbon Leadership Forum for their meticulous approach to carbon accounting, which showed that the project will be responsible for up to 80 per cent less carbon emissions than if it had been constructed using traditional techniques and materials. Third Space Commons also serves as the team’s entry into the U.S. Department of Energy Solar Decathlon Build Challenge, an international competition held to celebrate innovative and high-performance housing design.
More about Hempcrete;
Quality assurance in hempcrete construction can be achieved through various methods, including on-site testing during and after installation. One common way to ensure quality is through the use of moisture meters to monitor the moisture content of the hempcrete mixture during installation. This is important because if the mixture is too wet or too dry, it can affect the strength and durability of the finished product.
Once the hempcrete has been installed, additional testing can be performed to ensure the material has achieved the desired compressive strength. This can be done through the use of compression testing machines, which apply pressure to a sample of the hempcrete and measure its resistance.
It is also important to follow proper installation techniques and ensure that the hempcrete is compacted properly and allowed to cure for the appropriate amount of time. This may require specialized equipment, such as pneumatic tampers or vibrating tools, to ensure proper compaction and adhesion of the hempcrete to adjacent materials. Finally, ongoing maintenance and monitoring can help ensure the long-term performance of hempcrete structures. This may include regular inspections for moisture damage or other issues, as well as periodic reapplication of protective coatings or sealants to maintain the material's durability and resistance to weathering.
The US Hemp Building Association has announced that hempcrete has been approved for use in US residential building codes. This was approved by the International Code Council (ICC) and will take effect in 2024. However, building permitting departments can use the new code guidance now for proposed projects. Hempcrete has been used and approved in Europe for 30 years, but was not approved for US buildings until now due to the illegality of US industrial hemp until the passage of the 2018 Farm Bill.
https://ushba.org @hemp_building
Hemp cultivators:
The Canadian Hemp Trade Alliance (https://www.hemptrade.ca) provides resources and information for hemp cultivators in Canada.
The U.S. Department of Agriculture (USDA) (https://www.usda.gov/topics/hemp) provides information on hemp cultivation in the United States.
In terms of construction costs, benefits, and disadvantages, here are some key points to consider:
Benefits:
Hempcrete is a natural, sustainable building material that is renewable and biodegradable.
Hempcrete has excellent thermal performance, which can result in significant energy savings over the lifetime of a building.
Hempcrete has good acoustic performance, which can improve indoor comfort and reduce noise pollution.
Disadvantages:
Hempcrete has a lower compressive strength than traditional concrete, which can limit its use in certain structural applications.
Hempcrete is a relatively new building material, which can make it difficult to find experienced contractors and obtain necessary permits and approvals.
Hempcrete may not be suitable for all climates or building types, and additional insulation may be necessary in some cases.
Construction costs:
The cost of Hempcrete construction can vary depending on factors such as location, design complexity, and availability of materials.
Hempcrete can be more expensive than traditional concrete in some cases, particularly for smaller projects.
However, Hempcrete construction can be cost-competitive with traditional construction methods in larger projects or in locations where traditional building materials are expensive or difficult to obtain.
Here are a few USA and Canadian based companies involved in the hempcrete industry:
Hempitecture - Idaho https://www.hempitecture.com @hempitecture
Hemp Technologies - North Carolina https://hemptechglobal.com @HempTech
American Lime Technology - New Mexico http://www.americanlimetechnology.com
HempWood - Kentucky https://hempwood.com @hempwood
HempStone - Florida https://hempstone.net @hempstonellc
Hempcrete Natural Building - British Columbia https://www.hempcrete.ca @Hempcrete
Just BioFiber Structural Solutions - Canada http://justbiofiber.ca @justbiofiber
Canadian Greenfield Technologies - Alberta https://canadiangreenfield.com @CdnGreenfield
Canfiber - British Columbia https://canfiber.com @Canfiber
Bio Fiber Industries - USA https://www.biofiberindustries.com/pages/build
Overall, while Hempcrete is still a relatively new building material, studies suggest that it can be cost-effective and provide significant environmental benefits compared to traditional construction methods. However, careful consideration of the specific project requirements and available resources is necessary to determine the suitability and cost-effectiveness of using Hempcrete in construction.
Looking for more info?
There are numerous sources for detailed information on Hempcrete, including books, research papers, and online resources.
The ASTM International has established a subcommittee to develop standards for Hempcrete. New Guide for Hemp Hurd and Blast Fibre Intended for Selected Manufacturing Use https://www.astm.org/workitem-wk78707
The Future is Hempcrete https://metropolismag.com/viewpoints/building-with-hemp/ @MetropolisMag
Carbon negative & non-toxic Hemp Insulation https://www.usgbc.org/education/sessions/carbon-negative-non-toxic-hemp-insulation-12023510
Building with Hempcrete https://undercoverarchitect.com/podcast-building-with-hempcrete-jo-dalo-the-hemp-building-co/
The Hempcrete Book: Designing and Building with Hemp-Lime" by William Stanwix and Alex Sparrow https://www.worldcat.org/title/hempcrete-book-designing-and-building-with-hemp-lime/oclc/893685326
"Hempcrete Construction: A Comprehensive Guide" by Chris Magwood https://newsociety.ca/books/e/essential-hempcrete-construction
The International Hemp Building Association (IHBA) website, which provides information on the latest research, building codes, and case studies on Hempcrete construction projects. https://internationalhempbuilding.org
Hempbuild Magazine https://www.hempbuildmag.com/home/best-books-about-hemp-building @hemp_build
A 2020 study conducted by the University of Manchester found that Hempcrete construction can be more cost-effective than traditional construction methods in certain circumstances. The study found that Hempcrete construction was particularly cost-effective in buildings with complex designs or in locations with limited access to traditional building materials.
Out-of-plane strengthening of adobe masonry using hemp fibre ropes: An experimental investigation https://pure.manchester.ac.uk/ws/files/199779180/Abdulla_et_al_Eng_Struct_Oct21.pdf
A study conducted by the University of Bath found that Hempcrete construction can be cost-competitive with traditional construction methods. The study found that the cost of building with Hempcrete was comparable to the cost of building with traditional masonry, and that the energy efficiency of Hempcrete buildings can result in significant long-term cost savings.
The use of bio-based materials to reduce the environmental impact of construction https://researchportal.bath.ac.uk/en/publications/the-use-of-bio-based-materials-to-reduce-the-environmental-impact https://purehost.bath.ac.uk/ws/portalfiles/portal/101417869/CMSS_1.pdf
Regionalized Life Cycle Assessment of Bio-Based Materials in Construction; the Case of Hemp Shiv Treated with Sol-Gel Coatings https://www.researchgate.net/publication/335853181_Regionalised_Life_Cycle_Assessment_of_Bio-Based_Materials_in_Construction_the_Case_of_Hemp_Shiv_Treated_with_Sol-Gel_Coatings
Hempcrete - modern solutions for green buildings https://iopscience.iop.org/article/10.1088/1757-899X/1242/1/012021/pdf
Thanks for reading!
Business Enquiries;
rodmountainmedia at gmail.com
Reply